For those interested in reducing their carbon footprint and the amount of waste they create at home, a zero-waste lifestyle provides a practical approach to sustainability. However, zero waste means more than simply refusing plastic bags or composting food waste on an individual level.
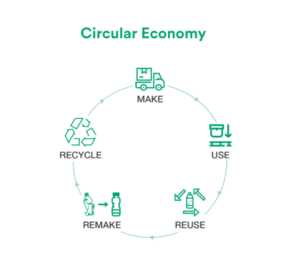
Source: rts.com
The ultimate goal of zero waste is to develop and promote a more circular economy through the redesign of products to reduce their environmental impact, as well as improve end-of-life management through extended producer responsibility (EPR). In short, the concept of zero waste must also extend to the manufacturing sector, with increased responsibility on producers to design waste out of the loop before consumers have to deal with it.
Achieving zero waste in manufacturing is a challenging prospect. Today, linear production methods that prize profit over sustainable production are everywhere—from the ubiquity of single-use plastics in packaging to the multi-trillion dollar fast fashion industry. How can zero-waste manufacturing become more prevalent? To better understand how reducing waste materials before they enter the consumer market is the key to achieving zero waste to landfill, we’re going to explore:
- What are Zero-Waste Manufacturing and EPR?
- Waste Reduction Through the Use of Machinery
- Waste Reduction Through Process Changes
- Reducing Manufacturing Waste Through the Choice of Materials
- Waste Recovery and Reuse in Manufacturing
- Extended Producer Responsibility
- Win-Win Scenarios Through Collaboration
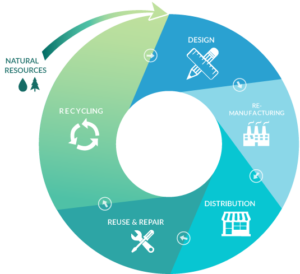
Source: rts.com
What are Zero Waste Manufacturing and EPR?
Zero waste in manufacturing is the movement to implement more sustainable practices across the entire production and supply chain. This doesn’t mean only removing waste at the point of production, but thinking instead about the entire lifecycle of a product – from how waste is created in the acquisition of the raw materials to what happens to a product and its packaging once it’s “consumed” and disposed of by the customer.
Among the driving forces behind this new approach to manufacturing is extended producer responsibility (EPR), a concept designed to place the responsibility for waste disposal creation back into manufacturers’ hands, rather than those of the consumer. EPR is a key part of zero waste, focusing on take-back and recycling programs for products, setting up collection points and recycling pickups for products, and perhaps most importantly, designing new products that are easier to reuse, repair, and recycle.
Reducing Manufacturing Waste with Machinery
Much of modern manufacturing is automated, and this offers the potential to deliver significant waste reductions when implemented correctly. On-demand packaging solutions, for example, are gaining traction within e-commerce. These machines build boxes according to the shape and size of a product, or even a group of products, as opposed to using off-the-shelf packaging.
This helps reduce excess card, paper, or plastic padding use, subsequently minimizing manufacturing waste to landfill. Shipping tiny items in massive boxes has become commonplace and is an example of how bad manufacturing systems can create waste further down the line, putting the burden of sustainable disposal onto consumers.
Additionally, the machinery used to produce goods can have a significant impact on achieving zero waste in manufacturing. One clear example of this is from Heinz in 2014. It used plastic bag-lined paleocons as intermediary storage for their sauces between the production and packaging plants.
These bags were being sent to landfill along with residual products after just a single-use, with no way to recycle them. Heinz made the switch to bulk holding tanks and reduced the number of plastic liners being used by more than 3,000 in only a year, as well as saving more than 44 tons of product from being sent to landfill.
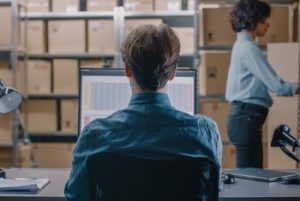
Source: smallbusiness.chron.com
Manufacturing Waste Reduction Through Process Changes
Not all changes within zero waste systems are as drastic as overhauling expensive machinery, however, since simple switches can make a huge difference. For example, better inventory management can help manufacturers acquire only the necessary raw materials when needed and in non-excessive quantities to prevent stock sitting around warehouses and factories, increasing the chances of damage, expiry, and eventually waste.
Systems that better understand demand also allow manufacturers to ensure excess product inventory is minimized. These processes should examine how the inventory is tracked and labeled, since many materials can be overlooked until they go past their expiry dates, wasting resources and money. This can be done in a variety of ways, with inventory tracking systems leveraging the latest technologies to manage stock.
Similarly, audits should be carried out at production locations to measure less obvious waste such as water and power. There are frameworks in place, such as LEED, that help businesses achieve waste reduction in these areas, along with specialists that can help walk manufactures through the process.
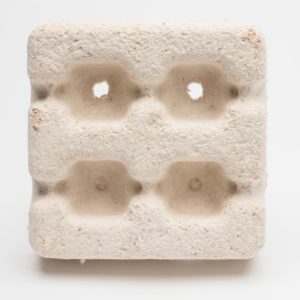
Source: ecovativedesign.com
Reducing Manufacturing Waste Through the Choice of Materials
Waste reduction through the choice of materials comes through changes to products themselves and, more commonly, changes to the packaging used to ship products. This can be as simple as designing new products that use less raw materials and natural resources to manufacture and increasing the amount of recycled material used in production.
For example, many companies are now using paper and cardboard where they would have used plastic a few years ago, relying on easily recyclable materials rather than complex, multi-material designs with plastic. This shows the full-lifecycle thinking that zero waste manufacturing requires.
Reusable packaging takes this one step further, looking at how product packaging can be kept in the production chain rather than disposed of after a single-use. Loop, for example, has been expanding globally and is based around delivering everyday items in reusable packaging—such as Häagen-Daz ice-cream in a metal tub.
A more extreme example of alternative packaging is the use of completely new resources such as compostable mushroom packaging. Currently, while these solutions have a few challenges, they do offer insight into how manufacturers hope to achieve zero waste production systems in the future.
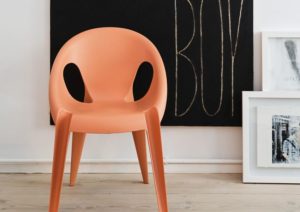
Source: homecrux.com
Waste Recovery and Reuse in Manufacturing
By the very nature of some manufacturing processes, it’s impossible to completely cut waste from production. In these cases, manufacturers must look at how waste products can be recovered, reused, and repurposed.
This could be within manufacturers’ own production chains by recovering and reusing raw materials for the same, or similar, products. For example, the Bell Chair from Magis is made of recycled polypropylene sourced from Magis’ own production waste, as well as that of the local automotive industry. This is a great example of how using producers’ own waste for new products can help bring companies closer to zero manufacturing waste to landfill through collaboration, as well as producing innovative and desirable products.
Alternatively, waste from production can be used as the raw material for entirely new products. The Veles cleaner, for example, is made from 97% food waste, which is a critical issue in waste management. Considering that food manufacturers assume a waste generation rate of about 5%, diverting this to new products would go a long way to zero waste in food manufacturing.
Similarly, waste products can be repurposed as useful tools for other production processes. For example, the use of coffee grinds as a growing medium for gourmet mushrooms, as GroCycle has successfully been doing in the United Kingdom for almost a decade.
A Win-Win Scenario Through Collaboration
As producers increasingly aim for zero manufacturing waste to landfill, we are seeing them intersect with other stakeholders in the fight for a more sustainable future. This is leading to interesting solutions to waste, such as the use of coffee pulp in forest recovery.
Researchers from ETH-Zurich and the University of Hawaii covered a piece of land with the coffee by-product and found that it helped create “a small forest in only two years” with 80% canopy (compared to 20% in the control) and trees that were four times as tall. Dr. Rebecca Cole, the lead author of the study, noted that since processing this waste would normally cost producers money, the use of the coffee pulp for reforestation is a “win-win scenario.”
The development of these innovative “win-win” situations is what will likely bring about truly zero-waste manufacturing systems since it delivers benefits to everyone involved at all stages of waste stream generation. Collaboration across the manufacturing sector then, is a key component of a truly zero waste system, allowing producers to find viable outlets for their waste which can subsequently become of use to another company.
Finally, as governmental organizations such as the EPA push for more sustainable manufacturing across the US, such as with its Lean Manufacturing business model, manufacturers will be increasingly accountable for the solid waste they create and the subsequent environmental impact. This may help drive collaboration across the industry, ensuring waste streams have a second life in new products.
For more information on achieving zero waste at your business or home, subscribe to zerowaste.com today. For a more in-depth look at how your business can go zero waste, arrange a chat with one of our TRUE Advisors now.